多年前,陶瓷色料企业乘借微粉砖等一系列通体陶瓷产品迅速发展的东风,疯狂而野蛮的在全国各地扩张,产量瞬间呈爆发式增长。据一位业内人士透露,在曾经的利润高峰时期,色料是当之无愧的暴利行业,稍具规模的色料企业“一天可赚取几辆奔驰车”。
喷墨印刷时代来临后,传统色料企业遭受了前所未有的巨大挑战,一些实力不济、产品链单一的传统色料企业因为墨水势如破竹般兴起、冲击而不得不面临着难以为继的危局。
尽管抛光砖仍是当前最主流的产品,坯用色料在未来一段时间里仍有较大市场,但在仿古砖、全抛釉、微晶石大肆膨胀的近几年,抛光砖市场占比持续下滑,坯用色料的未来之路毫无悬念也将会越走越窄。
釉用色料、胶辊色料是喷墨墨水一举崛起后的最大受害者。当国内外一批颇具实力的陶瓷色料企业相继开始着手喷墨墨水的研发、生产,曾经对陶瓷行业而言“犹如空气对人一般”重要的传统色料显得并不是那么重要了,部分传统色料可以完全被喷墨墨水所取代。
如何力挽狂澜,破解危局?部分颇具实力和基础的企业开始尝试向墨水生产转型,并且其中不乏成功者;部分企业选择了向墨水生产企业供应墨水生产所需的色粉和溶剂,成为陶瓷原料供应商的供应商……
不过,更多的企业却深陷迷茫之中,如何抉择,他们仍在艰难探索。
压力
2013年5月29日,广州琶洲展馆,魏明安静地坐在朋友公司近百方的展位上,一根接着一根不停地抽着香烟,一会儿工夫,面前烟灰缸里的烟蒂就已堆成了小山。
作为一家釉用色料的企业的老板,今年开年来魏明深感危机离自己越来越近。这次广州工业展上“处处都是和喷墨相关的产品”让他的心情变得更加沉重和复杂。
“这是我做色料这么多年来压力最大的一次。”魏明再次点燃一支烟,深吸一口向记者坦言。
这位做了十几年色料生意的中年男人,最早在佛山一家知名色釉料企业做销售,在积累了一定的资金和人脉后和朋友一起创业,开办了现在的公司。
多年前,陶瓷色料借住微粉砖等一系列通体砖风靡国内市场的东风和潮流,迎来了发展的黄金时期,随即以一种近乎疯狂的方式在全国各地野蛮扩张,魏明就是在那一段时期瞄准和抓住了机遇。
和他有着同样经历和曲折创业史的同行不乏其人,伴随着陶瓷行业一路走过的十余年里,他们事业有成,并亲身经历了行业的数次沉浮和艰难岁月——有金融危机的萧条,有产业转移的阵痛,也有国家楼市调控带来的寒冬。
2008年~2009年,因为金融危机和产业转移,色料行业大萧条,一些实力弱小和经营不善的企业相继在洗牌中死去,魏明也经历了一段难捱的日子。但随后产业转移带来的全国各地陶瓷厂遍地开花,又令色料行业看到了新的曙光。
“那次我熬过来了,不知道这次能不能挺住。”魏明告诉本报记者,墨水对釉用色料的冲击是致命的,他也一直也在思考转型,为自己谋出路。
2010年后,陶瓷喷墨印花技术开始在行业内大规模普及,时至今日已成一股不可逆转的潮流。业内保守估计,现在喷墨打印机数量在国内保有量已近千台。“根据目前市场需求状况估计,未来四年左右国内将迎来喷墨技术的高峰期,喷墨打印机数量将上升到6000~7000台,市场空间巨大。”广东陶瓷协会秘书长陈振广去年10月在公开场合曾发言预测。
一场轰轰烈烈的喷墨革命在行业内浩浩荡荡展开,各地陶瓷生产企业纷纷引进喷墨技术,进行瓷片、仿古砖生产线的改造。使用喷墨设备后的陶瓷企业,在化工原料的选择上开始摒弃传统色釉料,另寻墨水生产商合作。
若以此形势发展,“至少60%以上的色料将被墨水所取代。”景德镇陶瓷学院教授、佛山科捷制釉总顾问赵达峰向本报记者表示,墨水对传统色料的冲击非常之大,尽管现阶段某些深度颜色墨水还无法取代,但趋势已无可避免。
除此之外,相对于传统印花工艺,喷墨印花技术拥有着诸多不可比拟的操作便利。赵达峰表示,以往色釉料由于存在对版等人工操作的流程,在精准度的把握上存在一定误差,应用喷墨印花技术后,全部转化为机械化控制,人为干扰的因素可以基本消除,对色更为精准。
混乱的市场
经过三十多年的发展,我国已发展成为全球最大的陶瓷色釉料生产国和消费国,产品大量出口到世界各地。
但国内现有多少家陶瓷色料企业?陶瓷色料的年产量是多少?对于行业而言,这一直是谜一般难以给出确切数据的问题。记者曾就此咨询过行业内的诸多色料企业负责人,但无一能道出详尽的情况来。业内人士普遍认为,目前佛山地区颇具规模的色料企业有30多家,全国范围内的规模色料企业在100家以上。
一般而言,生产色料的化工企业,同时也或多或少的经营着釉料业务,相关行业协会和政府部门做形势分析时,通常将二者归为一体。
长期以来,色釉料行业属低门槛产业,在低投资、技术含量不高、环保要求不严的条件下,色釉料企业在全国各大陶瓷产区遍地开花,呈现一片蓬勃发展的繁荣景象。年销售5亿元的企业甚少,销售3亿元的就是大企业,多数小型、微型甚至连营业牌照都没有的色釉料企业依附在一些新兴陶瓷产区周边,零散稀疏地分布于全国各地,神秘而隐蔽。
另一方面,国家统计部门、行业协会也从未有陶瓷色釉料方面的权威统计数据,行业对陶瓷色釉料产能产值的统计只能以不科学的方式进行粗略估算,这使得国内色釉料企业的实际数量及产量显得迷雾重重。
据不完全统计,目前国内共有各种色釉料生产制造企业2000多家,其中规模以上的企业约500多家,主要分布在广东的佛山、潮州与山东的淄博。广东、山东两省的色釉料企业占全国色釉料企业总数的60%以上。
年产值仅为陶瓷产值8%~10%的色釉料行业,狭窄的市场却被2000余家企业共同瓜分,大量存在的小微型色釉料企业,一度让色釉料行业呈现出了“两千余人瓜分一块小蛋糕”的混乱、无序局面。
在近些年产业转移的浪潮下,一批生产规模较大、颇具实力的色料企业也相应开始在内地市场布局,并扎堆在规模相对较大的新兴陶瓷产区投资建厂或设立办事处。
一些将产品定位于三四级市场的新兴产区,大多数陶瓷企业为了实现利润最大化而严控生产成本,在色料产品的采购上,通常不会选择价格过高的优质产品,而是“谁的产品便宜,就用谁的”。
这使得一些新兴产区产生了不公平的合作关系和粗暴的竞争关系——陶瓷厂家刻意压低供应商产品价格、拖欠供应商货款,色料供应商刻意诋毁竞争对手的产品或者名誉。
一家广东色釉料企业湖北当阳办事处的业务人员告诉记者,早在2009年前后,湖北产区的上游配套行业发展较为滞后,将业务触角延伸至该地的色料企业数量十分有限,但如今却至少有十余家经营业务类同的色料企业在该地区竞争、角逐。
“不得不担心,突然有一天不知从哪冒出的竞争对手,以更低的价格将你的客户抢走。”这名业务人员说道。
危机
事实上,近几年来,色料行业因为混乱无序的市场竞争,暗藏着诸多潜在隐患。
过去,五颜六色的色料意味着财源滚滚。而现在,它们的利润越来越像白菜。
“1992年以前,国内还没有色料企业,产品严重依赖进口,1993年~1995年逐渐过渡,1995年~1998年如一股风潮,色料行业开始大发展。”据一位业内人士透露,在利润高峰时期,色料是当之无愧的暴利行业,8、9万元成本的色料可以买到100多万元,稍具规模的色料企业“一天可赚取几辆奔驰车”。
业内人士介绍,陶瓷色料有三大使用方向:坯用色料、釉用色料和胶辊色料。
喷墨印刷时代来临后,色料企业遭受了前所未有的巨大挑战。
喷墨技术的迅速崛起和墨水的大规模使用直接冲击和抢占了釉用色料和胶辊色料的市场占比,一些实力不济、产品链单一的传统色料企业因为墨水势如破竹般兴起、冲击而不得不面临着难以为继的危局。
坯用色料在未来一段时间里仍有较大市场,但在仿古砖、全抛釉、微晶石大肆膨胀的近几年,抛光砖市场占比持续下滑,坯用色料的未来之路毫无悬念也将会越走越窄。
抛光砖在独霸地砖江湖20年后,地位逐渐衰微,在建陶产品总产、销量的占比逐渐减少。曾有调查数据显示:抛光砖原有份额的近1/3已被仿古砖抢占,14个省会城市抛光砖销售额比去年下降10%。抛光砖市场份额正逐步被仿古砖蚕食,越来越多的企业开始放弃老本行进军仿古砖。
上世纪1990年代,抛光砖在巨大的市场需求刺激下,无论是技术装备、生产能力、品种规格、花色设计还是产品质量,都达到了世界领先水平,也成就了东鹏、诺贝尔、鹰牌等数十家一流品牌。
而2005年以来,抛光砖企业之间的互相抄袭仿制现象愈发严重,远没有意大利陶瓷企业争相创新的风气。一些领先企业每推出一款新品,不久在市场上便会四处泛滥。深受盗版困扰的东鹏董事长曾何新明表示,企业不去抓研发、抓设计,只知道搞“拿来主义”,这是市场混乱的主要原因,而这样的结果就是利润空间在不断下滑。
此外,追求个性和创意的80后消费者已经成为了当前主要的家居建材消费群体,伴随着经济的发展、生活水平的提升,人们对瓷砖表面的花色、图案、纹理提出了更高要求,而抛光砖恰在这些方面难以取得质的突破。
“仿古砖已经迎来快速发展的历史时期,虽不能说马上就能一枝独秀,但是配角的地位正在迅速改变,可能三两年内便可与抛光砖在市场上分庭抗礼。”曾有业内人士在接受媒体采访时表示。
抛光砖因产品严重同质化、创新裹足不前,正被陶瓷生产企业放弃,如2011年,淄博多数抛光砖企业转入仿古砖生产。两年后的今天,淄博企业再次改变产品结构,进行产品升级,现在他们正在做的事情是——大规模转产全抛釉和引进喷墨设备。
这些改变促使陶瓷砖产品的流行趋势正在悄然发生变化,国内色料行业原有的格局亦正在被打破,甚至是颠覆。
佛山市晋邦微晶科技有限公司一位销售负责人告诉记者,当前坯用色料在市场占比约为60%~70%,釉用色料约为30%,胶辊色料约为5%;但在未来的几年里,坯用色料或下降至35%左右,釉用色料和胶辊色料或上升至65%左右。
“这意味着,65%的色料将会被墨水取代。”该负责人表示。喷墨印刷相对于滚筒印刷而言非常节省色料,随着墨水的普及和大规模使用,色料企业的数量和产量必会同步减少。
出路
危机越来越逼近。
其实,在认识到发展困境和危机之后,一些积累了技术、人才和资本优势的色料企业也意欲转型。
当远泰制釉、万兴颜料、大鸿制釉、道氏技术、金鹰色料等少数一批色釉料企业相继在业内宣告已推出或拟推出喷墨墨水的时候,更多的企业却深陷迷茫之中,如何抉择,他们仍在艰难探索。
“色料企业的转型方向是要么做墨水,要么就做墨水生产所用的色粉和溶剂。”佛山市艾陶制釉有限公司技术部经理戴若冰表示,以前色料企业是直接将产品卖给陶瓷厂,但现在一些陶瓷厂家不需要了,它的唯一出路便是供给墨水企业。
然而,对于大多数企业来说,这两条路走起来并不简单。因为无论是生产墨水还是制造墨水所用的色粉,其中的几项关键技术对于大多数色料企业来说都难以攻克。
墨水生产需要用无机色料来发色,所需的色料细度是纳米级,但供应丝网印刷和胶辊印刷所需的色料细度是微米级,颗粒细度过大,不符合墨水所需色料的使用标准。
目前,国内色料的生产方式都是烧结而成,此种方式生产的色料产品颗粒粗、晶体大,远大于纳米级。而且当这种色料产品研磨到纳米级的细度之后,晶体易遭破坏,或无法发色、或发色很浅。
“现阶段国内大多数企业生产的色料还达不到墨水生产的使用标准,如果现在的企业是还是采用原先的烧结法,那么我估计想生产墨水的话会很难。”在戴若冰看来,摆在传统色料企业转型面前的一大障碍便是使用更为先进的色料生产方式。不过,其他诸如超声波等生产方式虽然更为先进,但生产成本、管理成本却要相对高出许多。
即便色料生产企业能够攻克这一难题,市场环境也不容乐观。曾经,有一位朋友给魏明提出建议:如果短期内做不出墨水,就去做墨水所用的色料,但随即这一建议就被魏明放弃了。
“因为现在国内墨水生产企业的数量很少,所需的色料也不多,并且这些墨水生产企业大多是从色料生产企业转型而来,本身就具备色料生产的技术和基础,能够自给自足。”魏明告诉本报记者。
而溶剂的生产同样需要解决一些细节问题,严格地讲,溶剂是一种介质。色料搅拌后,不会融掉成为液态,而是像沙子一样呈现颗粒状,细到纳米级以后,色料仍会沉淀,溶剂的作用便是让色料不容易沉淀。不过,溶剂一般为有机物,会发霉、变质、产生刺激性气味,这使得墨水的保质期不会很长,通常只有3~6个月。
这些都是色料企业在转型过程中需要直面和解决的问题。(文中魏明为化名)
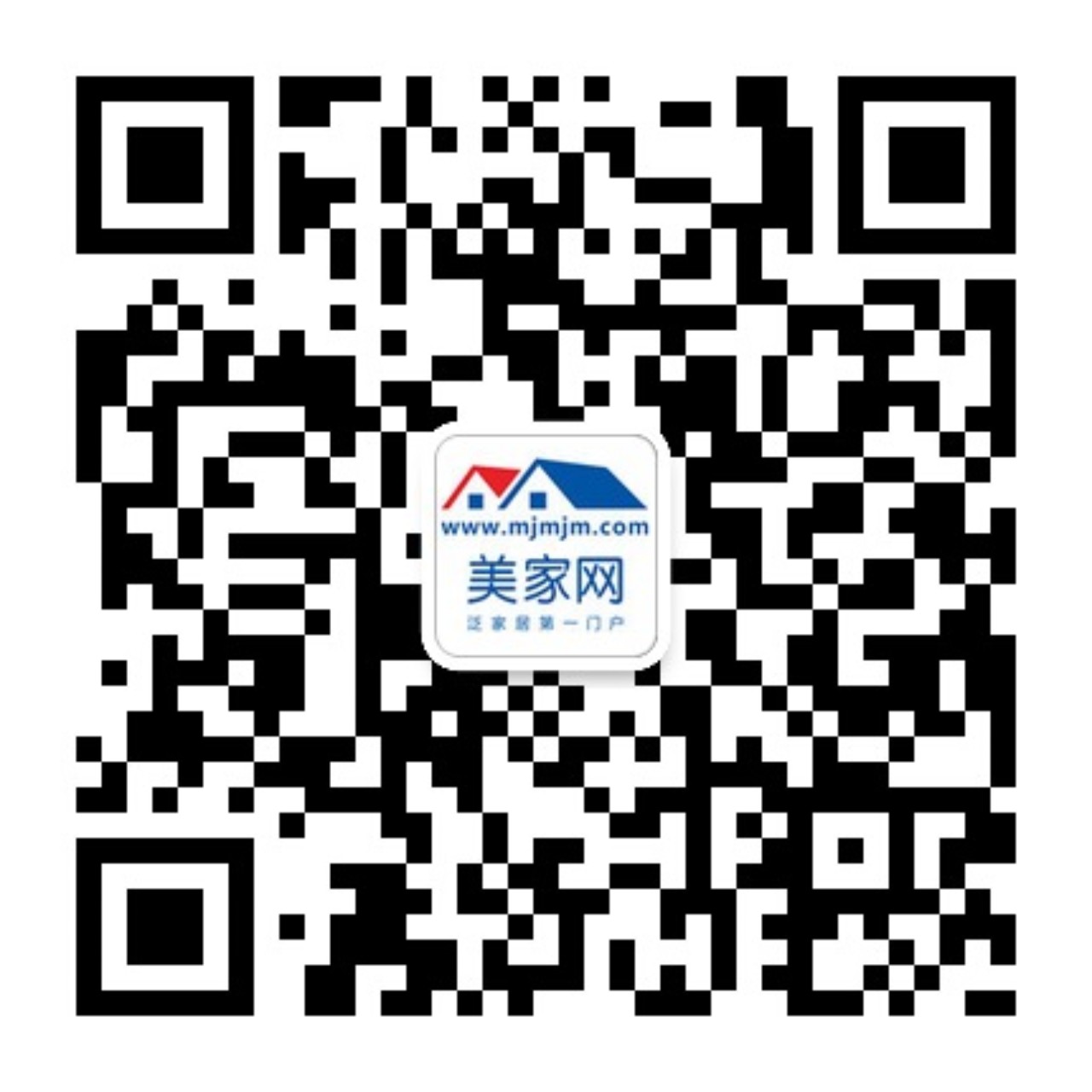