挤压成型技术是将加热至480℃的铝棒用机器推入模具,挤压成型后由出料口输出,通过使用不同模具,可以获得不同截面的型材。型材的出口温度与速度对于型材强度具有直接影响,通过检测型材出口温度及速度,能够更为有效地监控型材生产过程,提高产品质量。由于铝型材出口温度较高(>500℃),采用传统的接触式测量手段会产生较高的设备故障率,影响产品的连续生产。因此,目前国内铝型材挤压成型生产线普遍缺乏对于型材出口温度与速度的检测,无法进一步提高产品质量的可控性,加剧了质量波动性,降低了在国际高端市场上的竞争能力。因此,有必要综合使用光学器件与图像处理手段,设计非接触式高精度铝型材测速测温设备。由于测量设备与铝材表面非接触,具有故障率低,易于维护的优点。
永利坚铝业公司研发技术人员通过改进光学感应器的镜头和光源设计,提高了感应器的检测距离,以适应对表面高温的物体的运动速度检测。同时采用高速光学感应器,提高了检测的速度范围。利用图像采集处理平台,通过调度优化算法构建型材挤压形态分析专家数据库。可以方便技术人员随时调取库内资料进行分析,从而为生产质量监控提供可靠参考。通过实时检测铝型材的出料速度与出料温度,能够提高型材生产过程的控制能力,降低质量波动,提升产品竞争力。铝型材挤压设备智能化技术应用的研究具有重大的现实意义,增强铝型材生产过程的可控性,降低产品质量波动,采用非接触式方法实时在线检测铝型材的出料速度与温度,改进现有的粗放生产方式,能够稳定产品质量,提升企业竞争力。
该技术经国家专利局审核,于2015年11月授予发明专利。
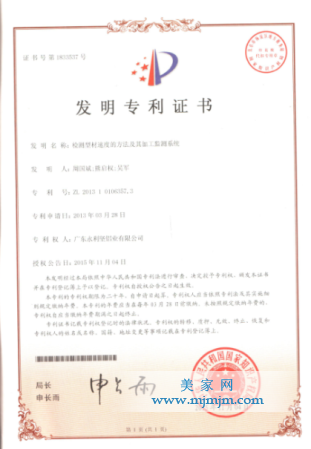
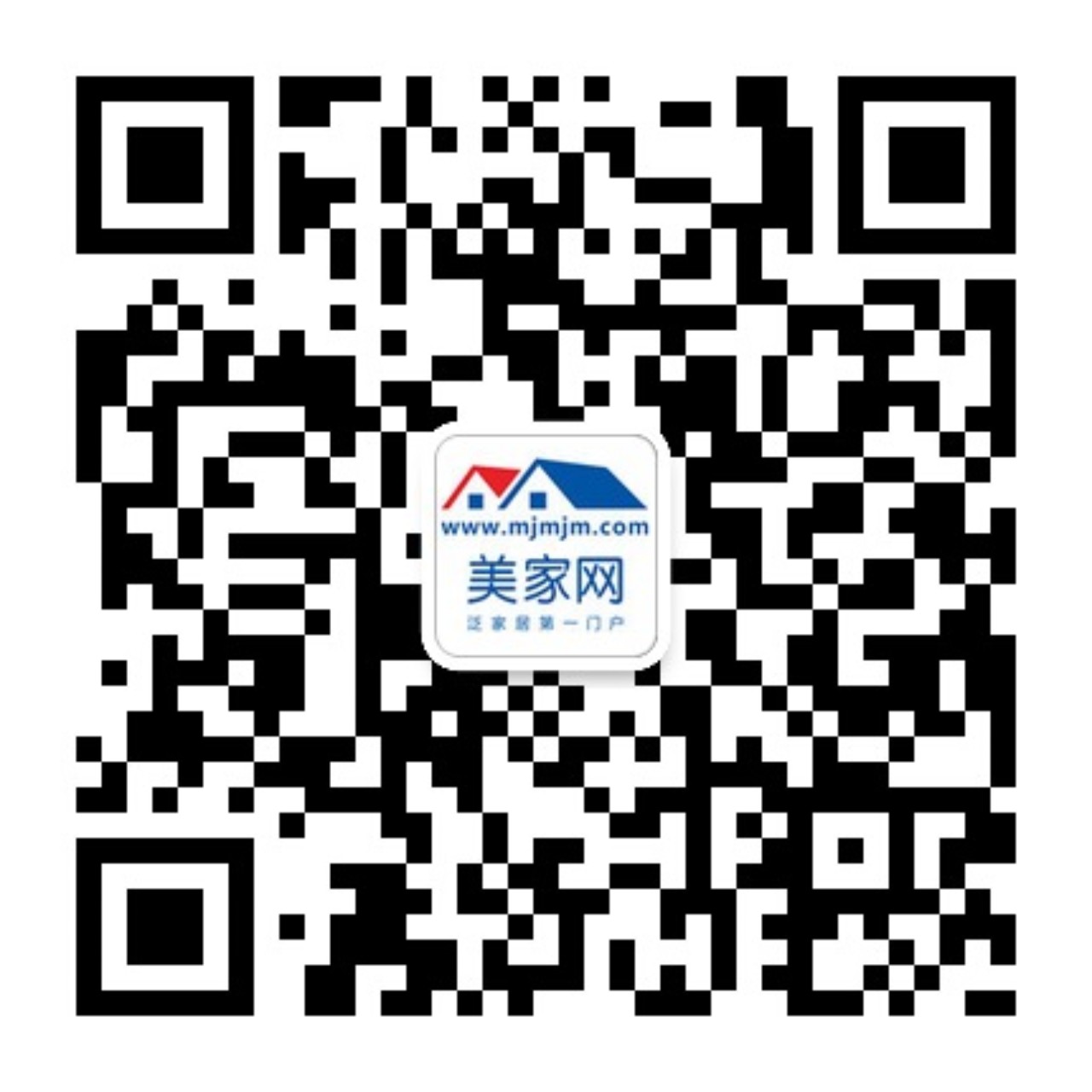