中国建陶包装工业1.0的形成
80年代中,欧洲现代化干粉制坯及辊道窑烧成技术大规模引进中国,开启中国建陶工业现代化时代。随着辊道窑技术进入中国,欧洲的瓷砖包装自动化技术也打开了中国的大门,但仅仅是昙花一现。
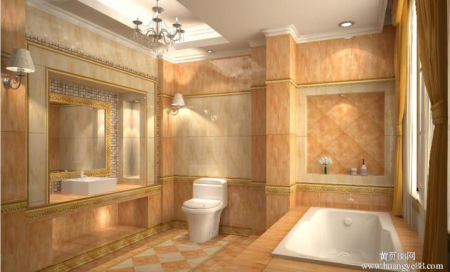
(图片源于网络)
欧洲的辊道窑和自动化包装技术都是全套的,当时中国引进的时候也是全套引进。原来制备、压机、窑炉、抛光等工序是无法用人来替代的,唯独在分选包装环节可以用人替代。也就是说,分选包装环节是可以用人也可以不用人的,但是为什么欧洲的自动化包装技术在中国昙花一现,引进之后没有得到很好地使用呢?有两个方面的原因:
第一,欧洲的自动化包装技术是和他们的物流环境相适应的,欧洲的生产线可以完全实现自动化,瓷砖垛在托盘上,再由托盘转移到叉车上,瓷砖从陶瓷厂的仓库运输到终端店面或者施工现场的过程中,也是用托盘来承载的。整个过程,砖包自始至终是不离开托盘的,而托盘是依靠机械叉车来搬运的。所以说,欧洲的自动化包装技术是建立在机械化物流环境基础上的。
反过来再看中国。当时的生产环境下,中国陶瓷生产几乎所有的环节都是依靠人工的,瓷砖也是依靠工人单包搬运,这就不可避免地对瓷砖包装的防护性提出较高要求。这就要求陶瓷厂在瓷砖包装箱中加入一些防护附件。而这些在欧洲的包装环节中是不存在的。因此我们从欧洲引进的包装线也就没有这些功能,想加入一些防护附件也无从下手。
所以,当时引进的自动包装设备即使能用,砖包搬运之后也会出现崩角、破碎等情况,自动包装技术也就被淘汰了。这也是欧洲自动包装技术在中国昙花一现的最主要原因。
第二,设备买回来肯定要维护保养,当时中国几乎没有自动化包装的配件工业,全都要依赖进口。如果零配件出了问题,陶瓷厂自己有库存还好,如果没有库存,就只能到国外去采购,其间的时间成本非常高。
那么陶瓷厂就不能保证这些零配件都有库存吗?理论上是可以的,但实际上还是有不少困难。相对于其他环节,分选包装环节的机械化程度比较密集,设备造价本身并不高,但是需要用到的零配件特别多,因此陶瓷厂如果要建立一个自动化元件的库存就显得压力很大。这样算下来,还不如直接用工人。
归结为一点,欧洲自动包装设备在中国昙花一现的原因,在于水土不服。而一个比较尴尬的情况又在于,即便是水土不服,当时国内的包装设备也全都是依赖进口,国产包装设备到了1988、1989年前后才开始出现。当时也只是研发一些比较简单的单机设备来代替进口设备。
2009年是中国建陶包装工业2.0时代的元年
2004年科达开始尝试重新引进欧洲自动化瓷砖包装技术开启国产化进程,到了2009年的时候鼎吉第一代独立式包装线进入市场,并成为当年唯一获得市场认可的自动包装线。在此之前,很多厂家也都尝试研究包装线,但真正被市场接受的只有在2009年的时候。因为2009年鼎吉包装线是真正得到市场接受与认可的,其表现为厂家推出试点,买家愿意接受其产品,从而买入后继的产品,其他商家看到这种情况,也开始向厂家购入该类产品。总的来说,就是有批量的订单,则说明其真正被市场所接受。
从现在的市场占有率来看,进口包装技术几乎是零。由于国外没有需求,所以不会投入这类研发。当时意大利也曾经尝试过该类研发,但是和我们国家相比,从需求的反向速度和成本来看,都缺乏竞争力。国外的产品不但进不来,其市场反而还被国内的产品所抢占。
从东南亚的市场来看,我国的产品正逐渐把外国的产品不断排挤。包括东南亚周边的南亚、中亚、中东等市场,这些地区以前都是西方设备的传统产区。但由于这些产区的发展历程和水平,和中国有很多类似的地方,他们所购买的欧洲设备也到了更新换代的时候,这时他们大都选择了到中国采购。比如,目前东南亚新的分选包装方面的需求当中,鼎吉占据了80%以上。
国内做分选包装设备的企业大概为十家左右,但在市场上形成竞争力的只有鼎吉和科达,科达的市场占有率排在第一位,鼎吉排在第二。
最近几年,陶瓷厂用工成本一直在攀升,这也给自动分选包装设备市场的拓展提供了机会。这就涉及到我们所说的“中国建陶包装工业4.0”的概念。目前陶瓷厂普遍的技术是停留在2.0和3.0阶段,2.0和3.0并不是全自动生产模式,从人工参与的程度上来看算是半自动生产模式,其最大的效果是降低了生产强度,但减少人工数量的效果并不太完美和彻底。
现在陶瓷企业用人的环境越来越严峻,产能也在向大品牌集中。以前的一些小企业对劳动保护法是无所顾忌的,大品牌则不然,他们很重视对劳动者权益的保障,这就导致劳动保护到达了一个较强的局面。减少用工,成为大品牌一个迫切需要解决的问题。
随着劳务环境不断进步和产能向大品牌集中,导致陶瓷生产在分选包装自动化方面,提出了一个更高的要求,这就是陶瓷包装4.0出现的背景。
从1.0到4.0,每个阶段都有其对应的代表性产品
包装机的1.0时代,代表性产品是捆扎机,这些设备是需要人工操作进行包装的,效率比较低,直到现在还有一部分企业将捆扎机作为自动包装的一个补充在进行使用。在鼎吉推出包装线之前,几乎所有的陶瓷厂都是用人工进行包装的。捆扎机的功能比较单一,只能被视为是一个单一工具。
2.0时代有了“生产线概念”(或称包装线概念)。这是鼎吉在2009年中国自动包装技术元年创造的,其旨在把整个包装的一些基本功能都基本完成,把很多单一的设备串联起来,可以成为一条生产线。但由于技术较为原始和初级,导致其适应的瓷砖的品类和规格较少,在机器出故障以后,对人的操作要求较高。2.0时代解决的是陶瓷厂包装劳动强度的问题,减少了很多生产步骤,大大地提高了生产效率。例如,原来每天有10吨的砖需要人工搬运放到托盘上,而现在有9吨可以实现自动化处理,剩下需要人去处理的只有1吨左右。2.0时代的包装设备在技术上有进步,但此产品在性能和工业收益上并不完善,还有待改进。
3.0时代没有一个很明确的时间点,但也可以提炼出两个标志性事件。第一个,是2011年鼎吉第一代用于人工分选分流后的单一品质瓷砖直连包装线堆垛生产线进入市场;第二个标志事件,是2012年标华第一代用于人工检验后的多品质色号瓷砖分选下载生产线(自动下砖机)进入市场。以前的包装设备只解决了包装的问题,没有解决分选的问题。此外,只解决了纸包的问题,而没有把叠砖功能的问题解决,到了2012年则解决了叠砖的功能问题。
4.0时代的包装线具有自动化分选、包装,及堆垛功能,可同时包装多品质色号的瓷砖。4.0首先是填补3.0的缺陷———瓷砖生产出来以后,无论是什么品质的都会连着包装线一起分选,从而真正实现包装和分选的全自动化生产线。其次,在陶瓷行业里,分选包装属于为数不多的技术比较精密的装备之一,对服务的依赖是非常大的,但陶瓷厂工人的从业素质却比较低,基于这样的矛盾,我们当时就提出了“保姆式服务”的概念,如果所有的服务都集中在一个地区,这种服务是可以做到的。但是自从2008年开始,由于环保要求越来越高,陶瓷厂开始分散外迁,导致“保姆式服务”难以实行,设备商不可能在每一个陶瓷厂旁边都设立一个服务点。为了解决这个难题,就需要用互联网技术把服务进行延伸,把原来依靠人服务变为依靠互联网服务,通过远程监控为客户进行技术上的指导,“保姆式服务”就变成了“专家式服务”。
4.0时代的包装线还有另外一个特征,就是智能化。目前虽然解决了分选包装环节的体力劳动问题,但智力化的劳动也要得到解决,否则仍然离不开人。那么智力劳动有包括哪些内容呢?这里面有两个方面,一方面是品质检验,比如釉面是否有气泡,是否有裂纹、崩边、崩角,色差的分辨等等,这些都得靠人工用肉眼来检查,而现在要靠智能视觉技术来解决;另一方面,是瓷砖生产车间的调度,过去的消费市场都有跟风心理。如金花米黄推出之后,广受大家的青睐,家家户户都有用。而生产的厂家也有从众心理,应市场的需求大批量的生产金花米黄。而现在的市场趋于个性化,大多数企业不喜欢跟风,有人认为有特色的产品才是好产品。追求个性化需求反馈到陶瓷行业来讲,从以前的以产定销变成以销定产。一个陶瓷厂存生产的几十种产品,怎样才能不引起混乱?所以,产品往生产岗的调度,仓库往商家的调度,市场间保持的有效沟通,就变成了一种全新的生产模式。这种生产模式的到来,使得原来一些靠人来解决的问题,现在得靠人工智能来解决。
中国建陶包装工业4.0时代从2016年开始
未来的4.0时代的包装设备和技术,必须具备一下特征:一是多规格兼容能力,二是最大程度的自动化,三是提供互联网售后服务的能力,四是人工智能技术的参与。多规格兼容能力主要是为了适应市场的多样化,自动化主要解决用工的问题。
包装技术的4.0,其方向与工业4.0是完全吻合的,陶瓷行业现在要思考的问题,是如何把具体的技术创新与工业4.0结合起来,而不是从一开始就站在一个非常宏大的层面来思考如何使工业4.0在陶瓷行业一蹴而就。
严格的说,自动包装和仓储是存在着一体性的,而目前的很多企业包装部门和仓储部门都是分开的。未来的发展,智能化也是需要统筹在一块的。国内的市场对于这种统筹只处于刚刚起步阶段,还需要一个完善的过程。国内市场要进入个性化,是导致自动包装和仓储一体化的重要先决条件。
1.0到2.0之间有个很清晰的分水岭,而2.0到3.0和3.0到4.0之间却很难以划分,因为这是一个量变到质变的过程,只能是给2.0、3.0、4.0三个阶段作一个定性。2.0是对1.0的一个否定,但3.0对2.0并不是否定,而4.0对3.0也不是完全的否定关系,2.0、3.0和4.0都是根据不同的客户群而存在的。对于1.0的存在,也有个别的陶瓷厂还是有少数需求的。可以明确的一点,是包装设备的4.0时代是从2016年开始的,但是2016年并不能称之为是“自动包装4.0元年”,因为最新的自动包装设备还没有形成持续、大批量的订单。只有客户掏出真金白银来持续购买设备才能证明4.0元年的出现,除此之外,不管是企业开新闻发布会也好还是技术鉴定会也好,都不能说明这一点,只有市场说了才算。
(作者系佛山市鼎吉包装技术有限公司总经理兼研发工程师)
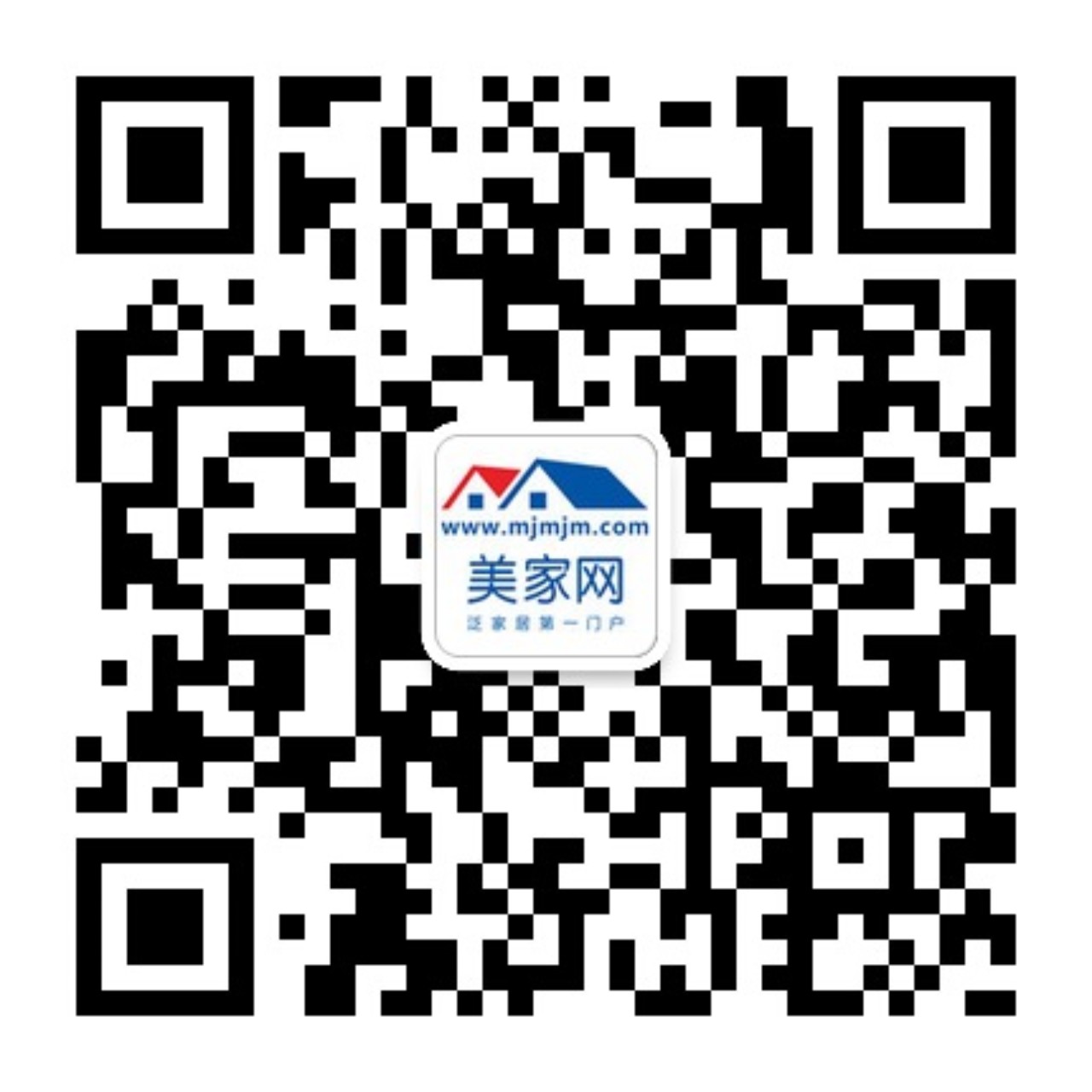